Designing a product to be easily manufacturable was not always a concern for designers during the earliest stages of engineering. As a result, prototypes that worked in the model shop couldn’t always be produced once they hit the factory floor. But research now shows that the vast majority of a product’s cost, quality, and manufacturability characteristics are determined in the earliest stages of product design. And in a time when time-to-market is critical, there is little or no room for a non-manufacturable part.
Fortunately, there are tools and processes available that take the burden off the designer while reducing overall part production cost. These are best viewed in the context of DFM or Design for Manufacturability. We spoke with Proto Labs engineer Tony Holtz to learn more about the benefits of DFM Analysis and to the designer — and their company’s overall manufacturing success.
Traditional product development used to be done in several stages. What changes occurred that made it necessary to rethink the product development process?
Well, I think this could be summed up by why our founder Larry Lukis began Protomold. In early product development, you could get simple prototypes but they took a long time and much longer for real injection molded components. The long delays added frustration as timely deadlines were missed and increased manufacturing costs continued to soar. His vision was to change the industry by reducing time and cost in bringing real injection molded components to the market place. He did this by automating the traditional manufacturing process by developing complex software that communicated with a network of CNC mills. This, along with quoting and design software, takes days and sometimes weeks out of the development stages and can be completed within just a few hours if not instantaneously.
How does DFM analysis aid designers in enhancing the manufacturability of their designs?
DFM allows designers to concentrate on designing their injection molded part while Proto Labs takes care of ensuring the part they are designing are manufacturable. I suggest having parts submitted for a DFM the first time you design the part, we don’t require the part to be perfect for injection molding such as wall thickness or draft. In the DFM, you obtain guidance on if side actions or inserts are required, what draft is needed for the parts, mold flow analysis so you can view potential thin areas or weak knit lines, ejector pin and gate placement among other important design suggestions.
What are the key benefits of DFM analysis?
Other than what I already mentioned, this can all be done within hours. So, when you design a part and submit it for DFM at the end of the day, many times you would have this feedback by morning so you can continue improving the design based on our guidance and functional requirements. Not only do you receive a DFM, but you obtain early cost justification to see if injection molding can justify your prototyping, bridge tooling or production needs. I have to mention one other thing here is that if you have very simply design changes. Proto Labs may decide to modify your parts design to make it more manufacturable for injection molding and send you the new design back to be reviewed before proceeding with an order. This process is called Proto Labs Proposed Revision.
At what stage in the design cycle should DFM be considered? Who in the product team should be included in the process?
I mentioned that this should be done early, often times during the first or second revision. But it can really be done at any stage in the process but it should be done early enough that if a design needs to be altered you have this time preventing you from missing your deadline or needing to expedite the order. This can’t always be avoided, but be assured that if you are in a hurry we can injection mold your parts in as little as 1 business day depending on size and part geometry.
Another good opportunity to utilize Proto Labs DFM is before you proceed to CNC machining and especially 3D printing. 3D printing can make amazing parts that can be utilized for prototype and occasionally end-use-parts, but if the intent is to injection mold these same parts you need to make sure they are manufacturable. Often times we see customers that don’t look at the end manufacturing process until they have spent thousands of dollars prototyping only to realize they designed something they can’t actually injection mold. This is a huge mistake as it only delays your project costing you thousands of dollars more to go through the same prototyping steps a second and sometimes third time.
Why are companies using DFM Analysis? Is this an in-house process or something that is best outsourced?
We are seeing more companies using DFM to free up designer time for the many reasons I’ve mentioned earlier. Companies are also wanting to keep more manufacturing state side and looking for alternatives to high-cost tooling when the demand is unknown and as product seems to be changing as fast as it is flying off the shelves. DFM at Proto Labs is completely free and there is no pressure to buy. So, you should be utilizing an external source for this, but don’t forget about what you already know, it got you to where you are today. We don’t intend to take away from your expertise and internal manufacturing processes, we want to help you when you need help whether that is in using our application engineers or simply as overflow.
Speaking of application engineers…we have more than a dozen application engineers that see more parts in a week than a lot of designers see in several years. They have experience in nearly every industry as Proto Labs doesn’t specialize in automotive, electrical design, medical or consumer goods — we specialize in manufacturing of injection molded parts, CNC machined parts and 3D printed parts.
What are the primary tools used in DFM?
Let me explain the process start to finish as easily as possible. Everything starts with the designer designing the part intended for injection molding. The designer then uploads the native file or exports an iges or step file directly to our secure website. They may be asked if this is for prototyping, production, estimated quantity, or material the parts are intended to be produced in. We take over from here and our proprietary software now takes that CAD and breaks it up into a million data points. A supercomputer analyzes each data point piecing it back together and creates a DFM and pricing just for you. This is returned back through a secure link in email or available in a project management account that the customer sets up.
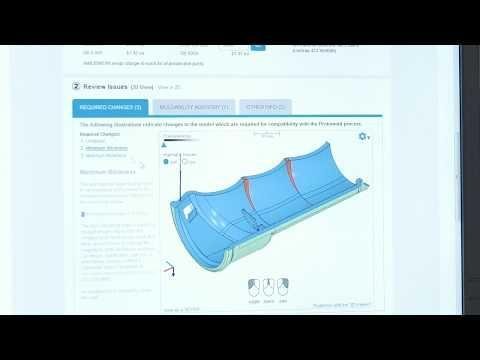
Tell us a little bit about your online quoting system, ProtoQuote. How does ProtoQuote help a designer interpret a design analysis and leverage their design for manufacturability?
Designing a part for injection molding can be difficult. How do you know what draft angles to use, if your part is too thick, thin or would the material you need the parts produced in even be able to fill your parts geometry? ProtoQuote helps guide a designer in simplifying a part by applying all of these aspects into the design. Our DFM has helped save thousands of dollars and time for designers of all levels, we work with students, people with an idea that may be on kickstarter, design firms and even the top fortune 500 companies with designers that have been doing this much longer than Proto Labs has been in existence.
Related resources:
Improving Manufacturability with ProtoQuote (webinar)
Leave a Reply
You must be logged in to post a comment.